By Kurtis Irwin, VP of Global Catalysis
Introduction
In the world of chemical engineering and industrial processes, reformer catalysts are the unsung heroes that make incredible transformations possible. These catalysts are the driving force behind reactions that convert hydrocarbons into valuable products such as hydrogen, syngas, and synthetic fuels. To ensure the reliability and direct the efficiencies of these catalysts, accurate durability testing is essential. In this blog, we’ll explore the critical role of reformer catalysts, the challenges they face, and why precise durability testing is a game-changer.
The Crucial Role of Reformer Catalysts
Reformer catalysts are at the heart of various industrial processes that impact our daily lives. Here’s why they are so crucial:
- Hydrogen Production
Hydrogen is a versatile energy carrier with applications in industries ranging from petrochemicals to transportation. Reformer catalysts play a pivotal role in producing high-purity hydrogen from hydrocarbon feedstocks like natural gas and naphtha. This hydrogen is then used in processes such as hydrogenation, hydrotreating, ammonia production, and fuel cells.
- Syngas Generation
Syngas, a mixture of hydrogen and carbon monoxide, is a fundamental building block for the production of a wide range of chemicals and fuels. Reformer catalysts enable the conversion of hydrocarbons into syngas, making it a cornerstone of the chemical industry.
- Sustainable Fuels
Reforming processes also contribute to the production of synthetic fuels, which can be an eco-friendly alternative to traditional fossil fuels. These catalysts are essential for transforming biomass and waste into sustainable transportation fuels.
The Challenges of Catalyst Durability
While reformer catalysts are incredibly valuable, they face several challenges that can impact their performance and longevity:
- High Temperatures
Reforming processes often occur at high temperatures, putting immense stress on catalysts. These harsh conditions can lead to catalyst deactivation over time.
- Impurities and Fouling
Feedstocks used in reforming processes may contain impurities that can poison or foul catalyst surfaces. Contaminants like sulphur compounds can degrade catalyst performance.
- Sintering
Sintering is the phenomenon where catalyst particles coalesce or agglomerate, reducing their active surface area. This can occur at elevated temperatures and result in reduced catalytic activity.
- Chemical Reactions
Catalysts can undergo chemical reactions with the reactants or products, altering their surface properties and deactivating them. Different surface alterations can occur, including surface poisoning, oxidation-reduction reactions, alloy formation, phase changes, and surface reconstruction. These transformations can ultimately lead to catalyst deactivation by modifying the catalyst’s active sites or altering its surface properties.
Given these challenges, it’s clear that reformer catalysts need to undergo rigorous testing to ensure they can withstand the demanding conditions of industrial processes.
The Significance of Accurate and Accelerated Durability Testing
Accurate and accelerated durability testing of reformer catalysts holds paramount importance in the realm of catalysis and industrial processes. These tests serve as a linchpin in ensuring the reliability, efficiency, and sustainability of catalysts, and their significance extends beyond mere validation. Here’s why accurate and accelerated durability testing is indispensable:
- Reliability Assurance
Testing allows manufacturers to verify the reliability of catalysts before they are deployed in industrial processes. It ensures that catalysts can meet the required performance standards consistently throughout their lifetime.
- Optimisation
Durability testing helps researchers and engineers optimize catalyst formulations and operating conditions. By identifying catalyst deactivation mechanisms, improvements can be made to enhance catalyst longevity.
- Cost Reduction
Reliable catalysts lead to fewer shutdowns and maintenance requirements in industrial plants, ultimately reducing operational costs. There is also a significant reduction in cost and time through accelerated ageing, particularly when a recirculating gas reactor setup is utilised.
- Environmental Impact
Efficient catalysts not only save money but also reduce the environmental footprint of industrial processes. Sustainable catalytic processes can lower emissions and minimize waste.
Advanced Testing Techniques
To meet the demands of accurate durability testing, advanced testing techniques have emerged in recent years. These techniques allow researchers to simulate real-world conditions and better understand catalyst behaviour. Some of these techniques include:
- Recirculating Synthetic Gas Reactors
Recirculating synthetic gas reactors provide a controlled environment where catalysts can be tested under continuous gas flow at required concentrations and at high temperatures. They enable researchers to closely replicate industrial conditions, leading to more realistic durability assessments.
- In-Situ Characterization
In-situ characterization techniques allow researchers to monitor catalyst performance in real-time. This provides valuable insights into catalyst deactivation mechanisms and the ability to make adjustments as needed.
- Computational Modelling
Computational modelling complements experimental testing by simulating catalyst behaviour under various conditions. This approach can help researchers predict catalyst performance and guide the design of more robust catalysts.
Conclusion
Reformer catalysts are the workhorses behind many industrial processes, driving the production of hydrogen, syngas, and sustainable fuels. To ensure their reliability and longevity, accurate durability testing is paramount. The challenges they face, such as high temperatures, impurities, and sintering, require precise testing methods to identify and mitigate potential issues.
Advanced techniques like recirculating synthetic gas reactors, in-situ characterization, and computational modelling are transforming the field of catalyst testing, enabling researchers and engineers to develop more efficient and durable catalysts. As we continue to push the boundaries of catalysis and sustainability, accurate durability testing will play a pivotal role in advancing the efficiency and environmental responsibility of industrial processes. In the end, it’s these unsung heroes, reformer catalysts, that help shape a cleaner and more sustainable future for us all.
Check out our blog ‘Reformer Catalyst Durability Testing – Applying a Recirculating Synthetic Gas Reactor’ where we specifically discuss durability testing in the OMEGA reactor, a highly efficient synthetic gas reactor up to 70% more energy efficient, reducing both costs and CO2 emissions.
CATAGEN’s purpose is to clean and decarbonise the air.
Bio – Dr Kurtis Irwin
Kurtis is the VP of Global Catalysis. He has over 10 years of experience specialising in after-treatment systems and catalysts. He is a Doctor of Philosophy (Ph.D.) focusing on mechanical engineering and he was recently awarded the UKRI Future Leader Fellowship award.
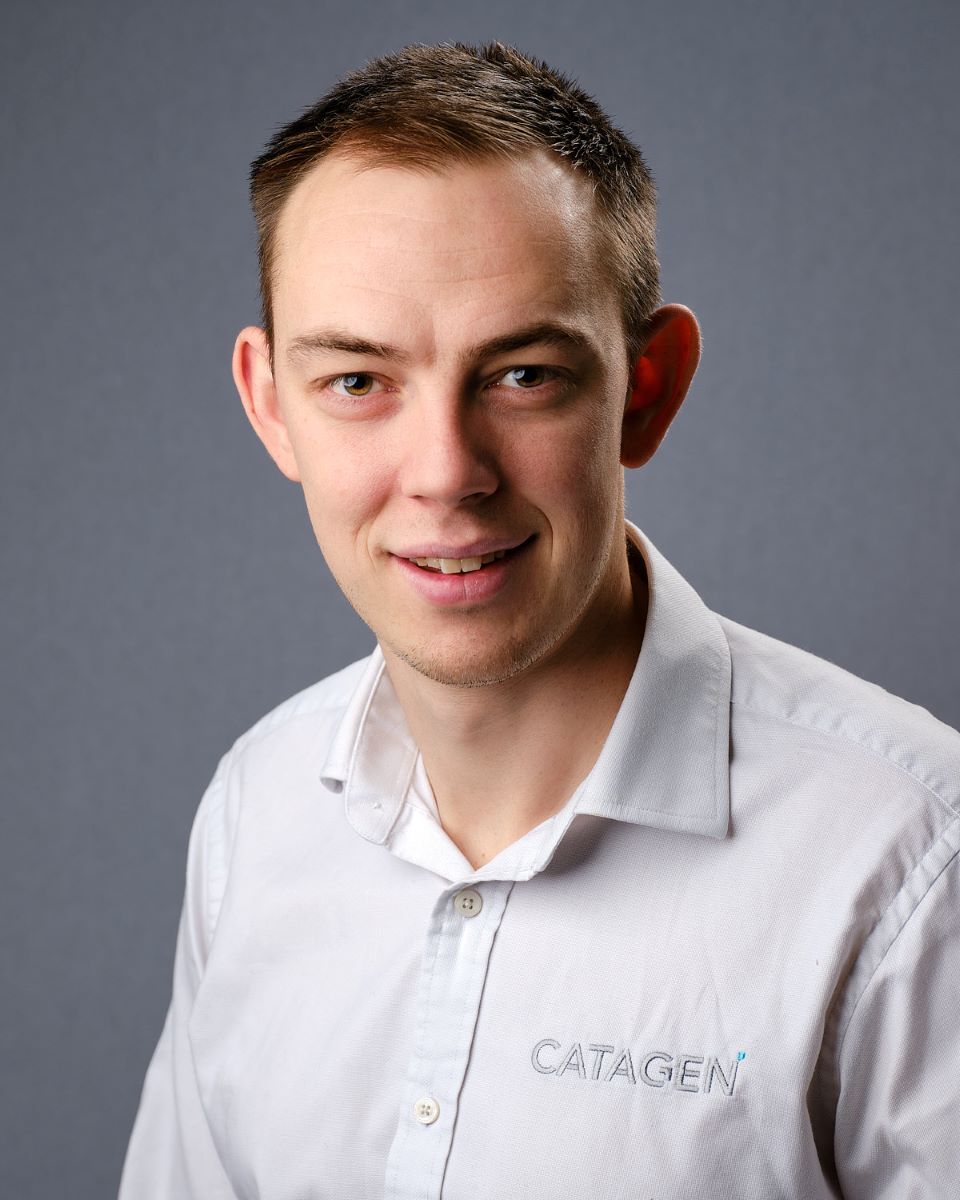