By Kurtis Irwin, VP of Global Catalysis
In today’s rapidly evolving energy landscape, reformer catalysts play a critical role in driving cleaner and more efficient industrial processes. These catalysts are essential for converting hydrocarbons into valuable products like hydrogen and synthetic fuels, underpinning countless applications across the chemical and energy industries. However, ensuring the durability and reliability of reformer catalysts remains a significant challenge due to the demanding conditions they face.
As industries push towards decarbonization and cost reduction, innovative testing solutions are required to validate catalyst performance under real-world conditions. In this blog, we’ll explore the challenges of reformer catalyst testing and how CATAGEN’s OMEGA recirculating synthetic gas reactor, coupled with advanced e-furnace technology, is transforming the way we approach durability testing.
The Vital Role of Reforming Catalysts
Reforming processes are pivotal in producing hydrogen, syngas, and synthetic fuels—key building blocks for a cleaner future. At the heart of these processes are reformer catalysts, often composed of metals like platinum, palladium, or nickel, supported on high-surface-area materials such as alumina. These catalysts facilitate the necessary chemical reactions, but their performance can degrade over time due to high temperatures, fouling, and chemical interactions, making rigorous durability testing crucial.
Challenges in Catalyst Durability Testing
Testing the durability of reformer catalysts presents several challenges:
- High Costs and Time Commitment: Testing under real-world conditions often involves high temperatures, pressures, and continuous hydrocarbon feeds, making the process both time-consuming and expensive. Extended aging periods, sometimes reaching 10,000 hours, lead to substantial gas consumption and associated costs.
- Complex Deactivation Factors: Catalysts can deactivate due to physical changes like sintering or fouling, as well as chemical processes that alter surface properties. Identifying the exact cause of deactivation requires precise testing under controlled conditions.
- Reproducibility Issues: Consistent testing conditions are vital for reliable results. Variability can lead to uncertainty, making it difficult to predict catalyst performance accurately.
- Environmental Impact: High gas consumption during aging phases not only increases operational costs but also contributes to CO2 emissions, adding financial and environmental strain.
To address these challenges, CATAGEN has developed the OMEGA recirculating synthetic gas reactor, a cutting-edge solution that enhances testing efficiency, reduces costs, and supports decarbonization.
Introducing the OMEGA Recirculating Synthetic Gas Reactor
The OMEGA reactor is a breakthrough in reformer catalyst durability testing, providing a dynamic and controlled environment that closely simulates industrial conditions. Here’s how CATAGEN’s OMEGA and e-furnace technology are changing the game:
- Continuous Gas Flow: The OMEGA reactor maintains a continuous flow of reactant gases, replicating real-world processes with gas flows ranging from 5g/s to 60g/s per catalyst sample. The reactor’s advanced recirculation capabilities reduce gas consumption by up to 75%, significantly cutting costs and emissions.
- Precise Control: With the OMEGA, you have complete control over gas composition and operating conditions, including temperature ranges from 200°C to 1000°C. This precision allows systematic studies of catalyst performance under varying conditions, with capabilities to test sulphur-sensitive catalysts and customize gas compositions down to parts per billion.
- Enhanced Monitoring and Flexibility: Advanced monitoring systems provide real-time data on catalyst performance, including continuous temperature and gas composition analysis. The OMEGA’s flexible design accommodates a wide range of catalyst sizes and configurations, from cored samples to full-scale monoliths.
- E-Furnace for Decarbonization: Integrating an e-furnace not only enhances temperature control but also significantly reduces CO2 emissions compared to traditional gas heating methods. This step forward aligns your testing processes with global sustainability goals.
The Advantages of Using the OMEGA Reactor
Adopting the OMEGA recirculating synthetic gas reactor offers numerous benefits:
- Improved Realism: By replicating industrial conditions, the OMEGA provides a realistic assessment of catalyst performance, allowing manufacturers to optimize catalyst formulations with confidence.
- Cost Savings: With efficient gas recirculation and reduced consumption, the OMEGA lowers operational costs and maximizes testing value.
- Reduced Environmental Impact: The e-furnace integration reduces CO2 emissions, contributing to greener testing processes and supporting broader decarbonization efforts.
- Enhanced Control: Precise gas composition control allows for in-depth studies of factors influencing catalyst deactivation, aiding in the development of more durable catalysts.
- Rapid Data Acquisition: Real-time data collection accelerates decision-making and deepens insights into catalyst behavior, helping drive innovation faster.
Conclusion
Reformer catalysts are the backbone of modern industrial processes, and their durability is key to ensuring efficiency and sustainability. CATAGEN’s OMEGA recirculating synthetic gas reactor, equipped with e-furnace technology, represents a leap forward in catalyst testing, offering a more realistic, cost-effective, and environmentally friendly approach.
Ready to revolutionise your reformer catalyst testing? Contact CATAGEN today to learn how our OMEGA reactor can enhance your testing capabilities, reduce costs, and support your sustainability goals. Let’s work together to drive innovation and create a cleaner, more efficient future.
Bio – Dr Kurtis Irwin
Kurtis is the VP of Global Catalysis. He has over 10 years of experience specialising in after-treatment systems and catalysts. He is a Doctor of Philosophy (Ph.D.) focusing on mechanical engineering and he was recently awarded the UKRI Future Leader Fellowship award.
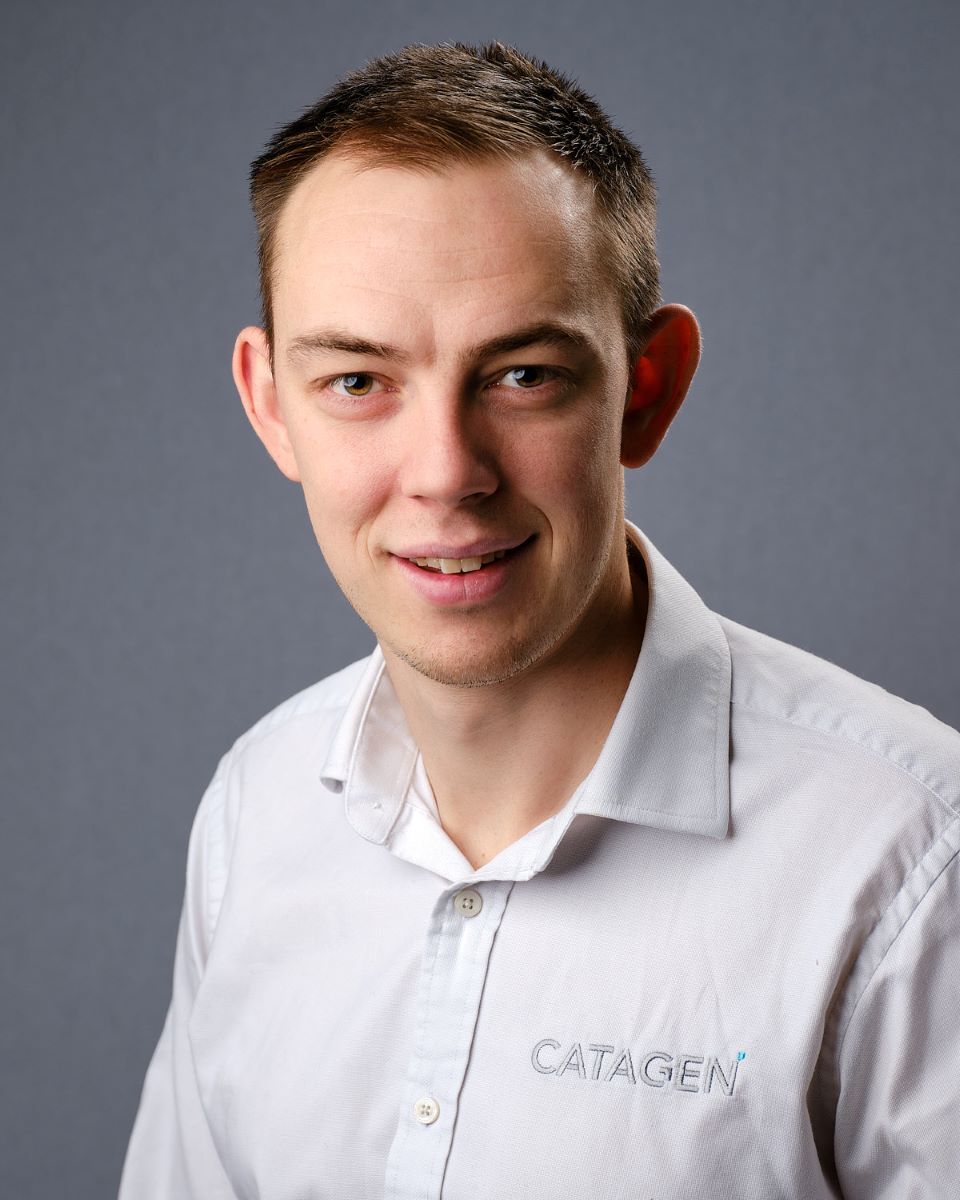